Transformer rewinding refers to the meticulous process of replacing the coil (windings) in a transformer. This service is essential when a transformer fails due to insulation breakdown, short circuits, or other electrical faults. Rewinding involves removing the old coil, manufacturing a new coil that matches the original specifications, and installing it into the transformer. This process not only restores the transformer’s functionality but also extends its service life.
Importance of Transformer Rewinding
Transformer rewind service is crucial for maintaining the efficiency and reliability of the system. It provides a cost-effective alternative to purchasing new transformers, especially for large, custom, or obsolete units. By rewinding, businesses can minimize downtime, reduce waste, and ensure the continuous operation of electrical equipment.
Types of Transformers That Require Rewinding
Power Transformers: Used in transmission networks for stepping up or down voltage levels.
Distribution Transformers: Employed in local distribution networks to provide voltage regulation.
Instrument Transformers: Includes current transformers (CTs) and potential transformers (PTs), used for measurement and protection.
Specialty Transformers: Such as isolation transformers, auto-transformers, and phase-shifting transformers.
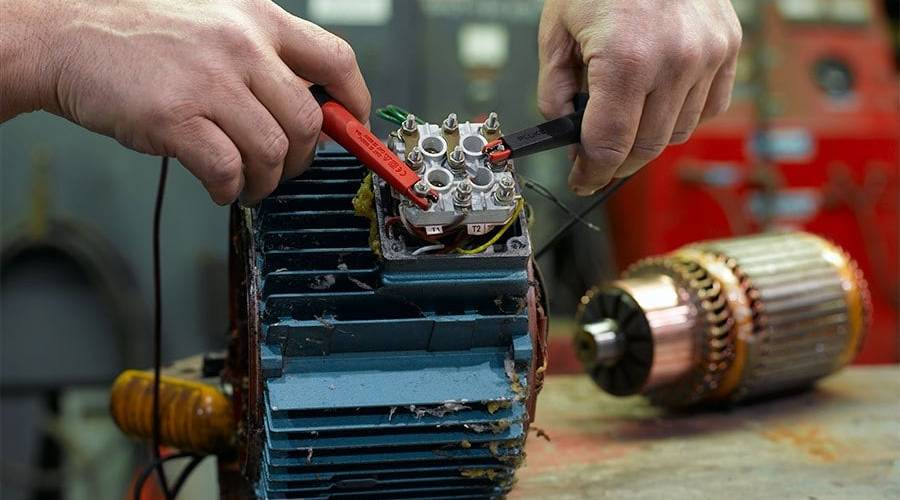
Tips to Identify Winding Problems in a Transformer
Unusual Noise or Vibration: Indicative of loose or damaged windings.
Overheating: Excessive heat can signal insulation failure.
Oil Leakage or Discoloration: Suggests internal problems, possibly related to the windings.
Electrical Performance Issues: Such as unexpected voltage drops or spikes.
Electrical Testing Methods to Detect Winding Faults
Insulation Resistance Testing: Measures the quality of insulation around the windings.
Turns Ratio Testing: Checks for discrepancies in the transformer’s winding ratio.
Sweep Frequency Response Analysis (SFRA): Detects winding deformation and displacement.
Short Circuit Impedance Test: Identifies changes in winding impedance that could indicate faults.
Safety Precautions During the Rewinding Process
Disconnect Power Sources: Ensure the transformer is completely de-energized.
Use Protective Gear: Wear appropriate safety equipment, such as gloves and eye protection.
Ventilation: Ensure adequate ventilation to avoid inhaling harmful fumes.
Follow Standard Procedures: Adhere to UAE industry standards and safety guidelines.
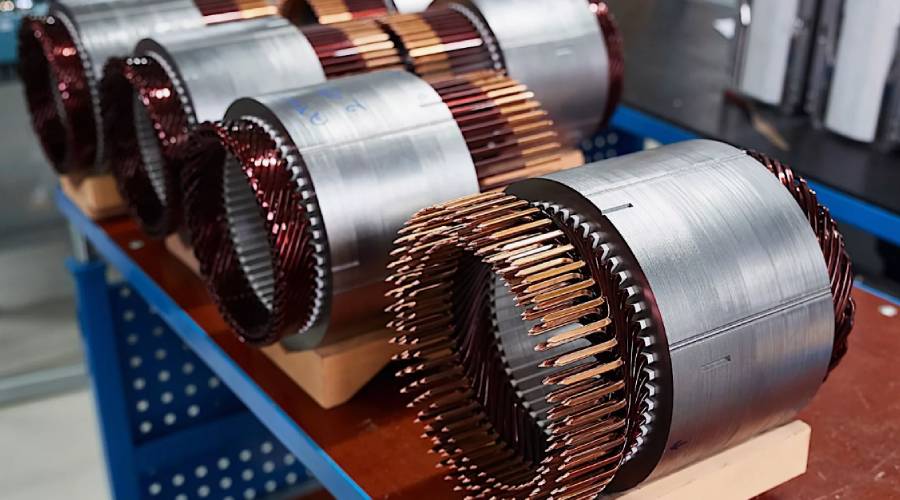
Significance of Proper Rewinding Techniques
The significance of employing proper rewinding techniques cannot be overstated when it comes to transformer maintenance and repair. Proper rewinding is essential for several reasons, each contributing to the overall efficiency, reliability, and lifespan of the transformer after the service has been completed.
Restoration of Original Performance
Transformers are designed to operate at optimal efficiency levels. Proper rewinding techniques ensure that the transformer is restored to its original performance specifications or better. This involves using high-quality materials, precise winding methods, and adhering to the original design parameters. Any deviation from these standards can lead to decreased efficiency, increased energy consumption, and a higher likelihood of future failures.
Ensuring Reliability and Longevity
The reliability of a transformer directly impacts the continuity of operations in industrial, commercial, and utility settings. Proper rewinding techniques contribute to the transformer’s reliability by ensuring that all components are correctly installed and that the winding is free from defects. This meticulous approach reduces the risk of unexpected breakdowns and extends the operational lifespan of the transformer, providing long-term value and stability.
Maintaining Safety Standards
Safety is a paramount concern in all electrical systems. Improper rewinding can lead to insulation failures, short circuits, or other hazards that pose risks to both personnel and property. By adhering to proper rewinding techniques, technicians ensure that the transformer meets or exceeds all relevant safety standards and regulations. This includes proper insulation, secure connections, and adequate testing post-rewinding to confirm the absence of electrical faults.
Compliance with Industry Standards
The electrical industry operates under strict standards and guidelines to ensure the safety, efficiency, and reliability of equipment. Proper rewinding techniques are aligned with these standards, ensuring that the transformer remains compliant with industry regulations. This compliance is crucial for certifications, insurance, and legal requirements, and it helps maintain the transformer’s warranty and insurance coverage.
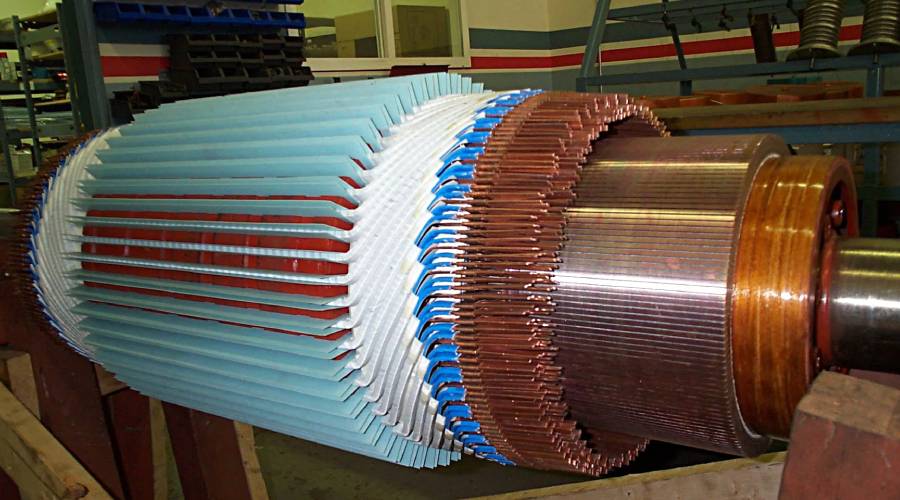
Energy Efficiency
In an era where energy efficiency is increasingly important, transformers play a crucial role in minimizing electrical losses. Proper rewinding techniques can even improve upon the original energy efficiency of a transformer by utilizing advanced materials and technologies. This not only reduces operational costs but also contributes to environmental sustainability by lowering energy consumption and greenhouse gas emissions.
Cost-Effectiveness
While the initial cost of rewinding a transformer may be significant, proper rewinding techniques ensure cost-effectiveness in the long run. By restoring the transformer to its optimal condition, businesses can avoid the higher costs associated with frequent repairs or premature replacement. Additionally, the improved energy efficiency and reduced downtime contribute to overall savings.
Customization and Upgrades
Rewinding provides an opportunity to upgrade the transformer to meet current or future needs. Proper rewinding techniques allow for the integration of modern materials and technologies, enhancing the transformer’s performance and adaptability. This could include better insulation materials, more efficient winding configurations, or adaptations to handle different loads or environmental conditions.
Cost Analysis of Rewinding vs. Replacing Transformers
When a transformer fails or shows signs of significant wear, decision-makers are faced with two primary options: rewinding the existing transformer or replacing it with a new one. The choice between these options involves a detailed cost analysis that considers not only the immediate financial outlay but also long-term operational costs and benefits. Here’s a deeper look into the cost analysis of rewinding versus replacing transformers:
Initial Investment
Rewinding: The cost of rewinding a transformer generally ranges between 40% to 60% of the price of a new equivalent unit. This percentage can vary based on the complexity of the rewind, the size of the transformer, and the specific requirements of the rewinding process. For example, rewinding a medium-sized industrial transformer might cost up to 10,000 AED.
Replacing: Purchasing a new transformer involves a higher initial investment, often double or more than the cost of rewinding. For the same medium-sized industrial transformer, a new unit could be of maximum 20,000 AED. depending on the specifications, manufacturer, and additional features.
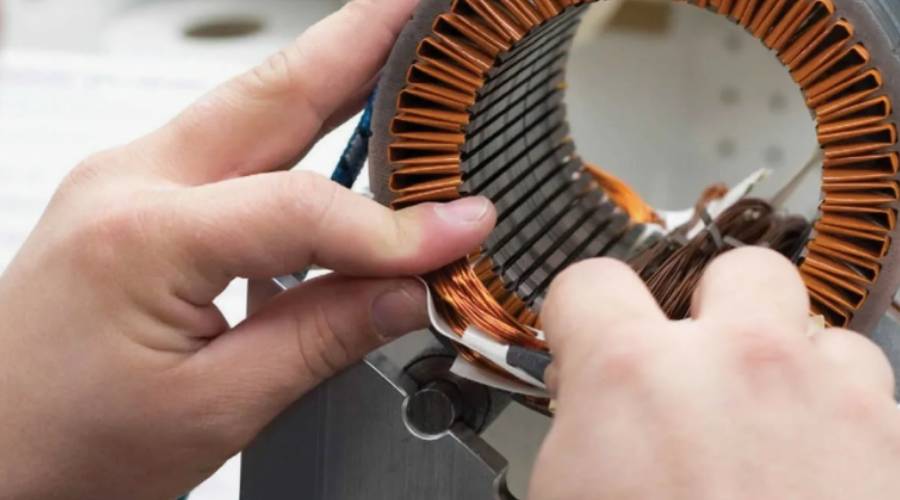
Downtime and Installation Costs
Rewinding: The process of rewinding can be time-consuming, especially for complex or large transformers. However, experienced service providers can minimize downtime through efficient practices and by scheduling work during planned outages. Additionally, since the existing transformer casing and infrastructure are reused, installation costs are generally lower.
Replacing: Replacing a transformer can also lead to significant downtime, particularly if the new unit has different specifications or requires modifications to the existing infrastructure. Installation costs can be higher due to the need for adjustments, new fittings, and potentially more extensive electrical work.
Operational Costs and Efficiency
Rewinding: If done correctly, rewinding can restore a transformer to its original efficiency or improve it if advanced materials and techniques are used. However, there’s a risk that a poorly rewound transformer may operate less efficiently, leading to higher long-term energy costs.
Replacing: A new transformer typically offers better efficiency, especially if replacing an older or outdated model. Modern transformers are designed with improved materials and technology, potentially offering significant savings in energy consumption and operational costs over time.
Environmental Impact
Rewinding: Rewinding is a more environmentally friendly option as it reuses existing materials and components, reducing waste and the demand for new raw materials. This aspect, while not directly affecting financial costs, can impact corporate sustainability goals and public image.
Replacing: Manufacturing a new transformer has a higher environmental impact due to the use of raw materials and energy. However, the improved efficiency of a new unit can mitigate some of these impacts over its operational life.
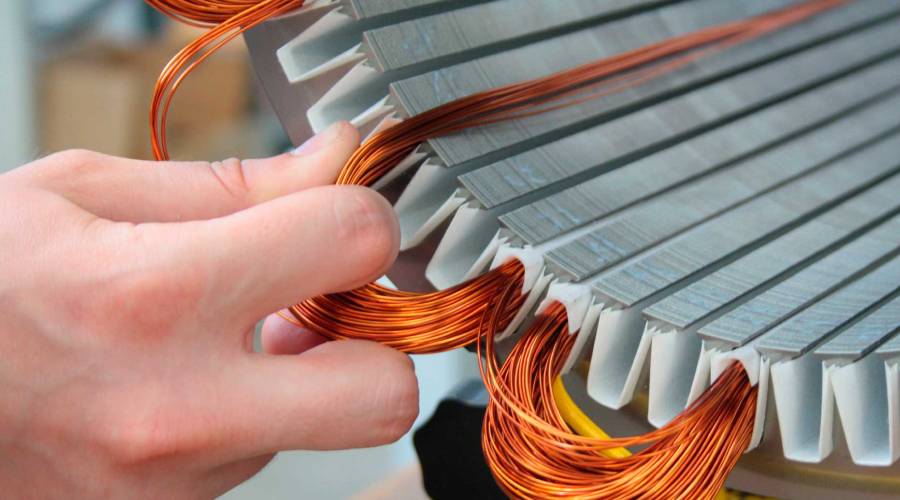
Preventive Maintenance Procedures to Reduce the Need for Rewinding
Regular Inspections: Schedule routine inspections to detect issues early.
Thermal Imaging: Use infrared cameras to identify hot spots indicative of winding problems.
Oil Analysis: Test transformer oil for contaminants and chemical properties.
Load Management: Avoid overloading the transformer to reduce stress on the windings.
Potential Challenges and Opportunities for the Rewinding Industry
Challenges
Technological Advancements: The rapid pace of technological advancements in transformer design and materials can pose a challenge to the rewinding industry. Staying abreast of these changes requires continuous learning and investment in new equipment and training.
Quality Control: Maintaining high standards of quality is crucial for the success of rewinding services. Inconsistent quality can lead to a loss of trust and business. Implementing and adhering to stringent quality control measures can be challenging but necessary.
Environmental Regulations: Increasingly strict environmental regulations regarding the disposal of old transformer components and the use of certain materials can impact the rewinding process. Compliance requires ongoing attention and adaptation to legal standards.
Competition from Manufacturers: Some manufacturers offer extended warranties or service contracts that can make the option of buying new more attractive than rewinding. Additionally, the decreasing cost of new transformers due to mass production and global competition can challenge the rewinding market.
Skilled Labor Shortage: The rewinding industry requires skilled technicians who understand the intricacies of transformer design and rewinding techniques. A shortage of such skilled labor can limit the capacity and growth of rewinding services.
Opportunities
Sustainability Trends: The global push towards sustainability and reducing waste presents a significant opportunity for the rewinding industry. By promoting rewinding as an environmentally friendly alternative to replacement, companies can tap into the growing market of eco-conscious businesses.
Customization and Specialization: There is a niche market for the rewinding of specialty or obsolete transformers where replacements are not readily available. By specializing in these areas, rewinding companies can create a unique selling proposition.
Emerging Markets: Developing countries and emerging markets present new opportunities for the rewinding industry. As these regions build and upgrade their electrical infrastructure, the demand for cost-effective solutions like rewinding will increase.
Service and Maintenance Contracts: Offering comprehensive service contracts, including maintenance, testing, and emergency services, can provide a steady income stream and build long-term customer relationships.
Technological Integration: Incorporating new technologies such as IoT sensors and remote monitoring into the rewinding service can offer added value to customers, enabling predictive maintenance and efficiency optimization.
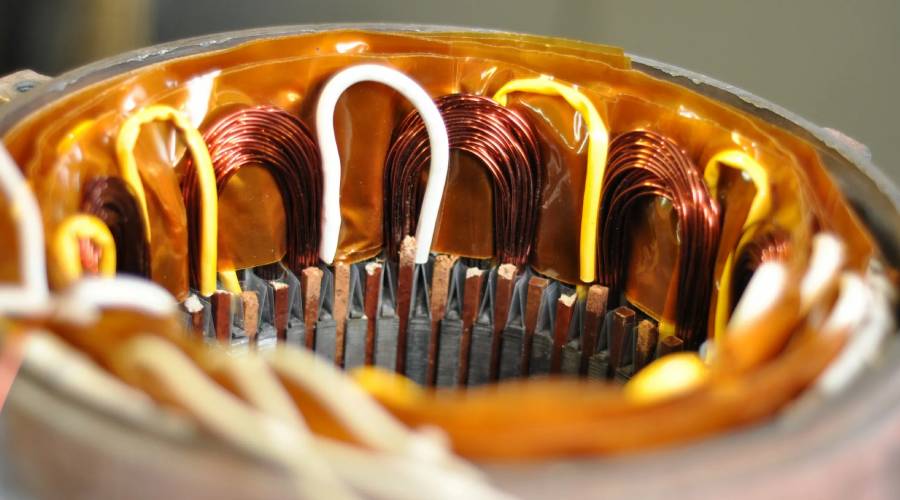
Innovation in Rewinding Techniques
Advanced Diagnostic Tools
The use of advanced diagnostic tools, such as thermal imaging cameras and vibration analysis equipment, can improve the accuracy of fault detection in transformers, leading to more targeted and effective rewinding.
Automated Winding Machines
The adoption of automated winding machines can enhance the precision and speed of the rewinding process. These machines can produce coils with consistent tension and alignment, reducing the likelihood of errors and defects.
High-Performance Insulation Materials
Utilizing new and improved insulation materials can increase the thermal, chemical, and electrical resistance of rewound transformers, extending their lifespan and enhancing their performance.
3D Printing
The use of 3D printing technology can revolutionize the production of custom parts and components for transformer rewinding. This can reduce lead times, lower costs, and allow for greater customization.
Eco-friendly Practices
Innovations in eco-friendly rewinding practices, such as solvent-free varnishes and recycling of old components, can help meet environmental regulations and appeal to sustainability-minded customers.
Online Monitoring and Analytics
Integrating online monitoring systems and data analytics into rewound transformers can provide continuous performance data, enabling predictive maintenance and early fault detection.
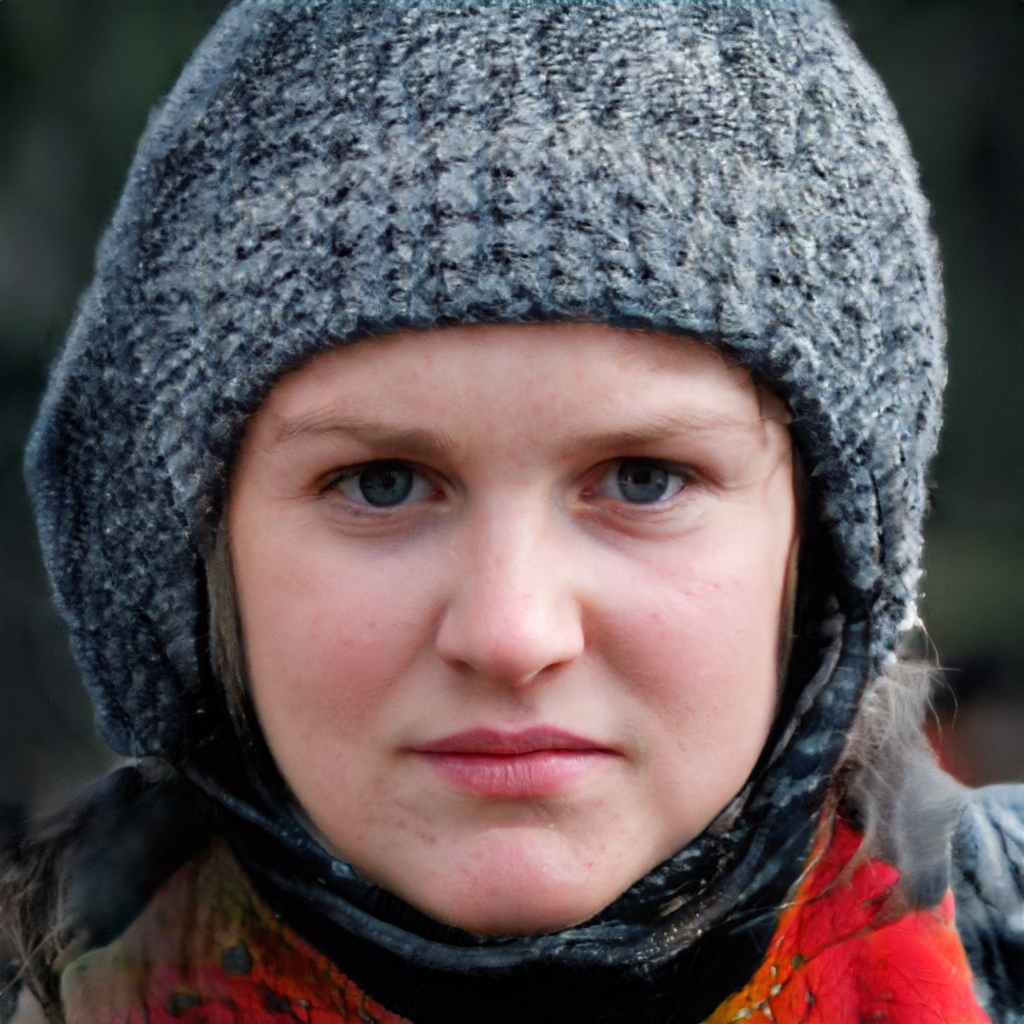
I am an accomplished coder and programmer, and I enjoy using my skills to contribute to the exciting technological advances that happen every day.